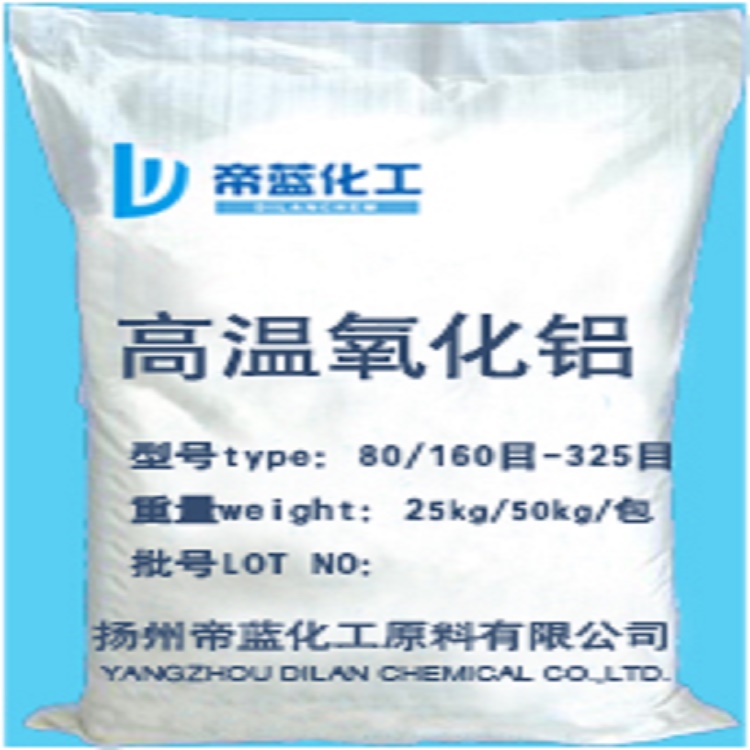
2、摘要:以水溶性的磷酸盐为主要成膜物质,铬酸(盐、酐等)为调节剂,球形铝粉为颜料合成了水基含铝耐高温防腐蚀涂料,该涂料具有优异的耐热、耐湿、耐盐雾、耐高低温冲击等性能。关键词:磷酸盐;耐高温涂料;防腐蚀涂料;铬酸;铝粉本文探索了水溶性磷酸盐作为主要成膜物质的水基耐高温涂料的制备条件。以铬酸(盐、酐等)作为调节剂,球形铝粉为主要颜料,制备了无机耐高温防腐蚀涂料。该涂料具有优异的耐温、耐湿热、耐盐雾、耐高低温、耐冷热冲击(500常温水,10个循环
3、)性能,是综合性能优异的涂料品种,被广泛应用于车辆尾喷管金属、换热器管壁等的长效保护。该产品至今仍被少数国外厂商控制,价格很高。水基含铝耐高温防腐蚀涂料最知名的牌号为SERMETELW,是美国TELEFLEX公司的专利产品,最早在1961年出现,当时该产品用于发动机叶片(不同等级叶片采用不同的金属材料)的长期防护。经过多年发展,形成了600多种系列涂料产品,并广泛用于长期工作温度为600700的高湿热环境的金属材料的保护。因该产品的技术思路十分特殊,只有少数国外厂商研制成功了该类产品。1.试验部分11原料试验用原料见表1。
4、表1原料名称、规格及产地12合成工艺磷酸与氧化镁在可控条件下反应,生成透明纯净的Mg(H2PO4)2,反应方程式如下:&
5、#160;Mg的磷酸盐有MgHPO4、Mg(H2PO4)2、Mg3(PO4)23种,只有Mg(H2PO4)2是水溶的,并具有在成膜过程中形成无机高分子的性能。在上述磷酸盐树脂中加入铝粉、铬酐及其他水性助剂,高速分散后过滤,最终制备成题述产品。13施工工艺将钢板(或其他金属板)工件仔细除锈、除油处理后吹干,将该涂料喷涂或刷涂后置于85烘箱中闪蒸05h,除去水分、溶剂等,然后将工件在3
6、45下预干燥05h。如涂层厚度不够可以重复上述工艺,最终将工件置于(550±10)下干燥2h即可。14水基含铝耐高温防腐蚀涂料的主要技术指标主要技术指标见表2。
7、;表2主要技术指标2结果与讨论21基料对涂料性能的影响虽然对于磷酸二氢盐在高温下的固化机理不十分清楚,但通常采用磷酸二氢盐作为无机涂料的基料。理论上H3PO4:MgO=2:1(克分子比),但是实际试验中测试结果并不完全相符涂料品牌网,往往过量的H3PO4对成膜有帮助。在其他条件一致的情况下,考察了
8、磷酸二氢盐制备过程中酸超量多少对涂料成膜性的影响(见表3)。
9、表3磷酸过量对涂膜性能的影响通过试验证实,过量磷酸有助于涂料与底材的附着,但是磷酸达到一定量后可能过早或过多地与底材金属反应,形成连续的氧化钝化层,阻止了树脂与底材的螯合等反应,造成了成膜性的下降;此外艺术涂料制备,在涂料高温固化过程中,超量的磷酸及产物磷酸二氢盐不但与金属基材反应艺术涂料制备,而且对球形铝粉表面的氮化层、氧化层的破坏具有积极影响,提高了液态铝的融合、扩展、流平等,并提供铝膜与底材的附着力。22铬酐和铬酸钙的影响
10、铬酐的作用是提供给涂料体系一定量的强氧化剂,与磷酸等配合来钝化存在于涂料水溶液中的铝粉,提高贮存稳定性;同时在固化过程中与不同的材料(铝粉中的铝、底材中的不同金属甚至是与聚合过程中的聚磷酸盐)发生反应形成大分子化合物,有利于涂层的形成。加入铬酐的作用很复杂,过量引入会与过量加入磷酸一样,引起铝粉的过度钝化,对涂层的形成不利,为了降低铬酐对酸值的影响,在涂料中加入适量的铬酸钙,并获得了良好的效果。有资料显示固化后的铬离子50与金属底材结合,35与铝粉结合,10与镁结合,从而可以确定铬酐钙的加人对涂层的附着力贡献突出。铬酸钙的加入对涂层的影响见表4。
11、
12、表4铬酸钙对涂层的影响试验证明,铬酸钙主要为提供涂料六价铬离子,在高温下活泼的化学性质使其有明显的螯合作用,可以提高涂层的附着力等性能。过多的加入铬酸钙在固化过程中容易引起气泡等弊病,需控制其用量。铬酐通常用于化学电镀和金属钝化处理,近年来有研究显示铬酐有可能引起癌变,因此国外已经禁用。考虑到这一因素,希望通过高锰酸钾替代铬酐,但是采用高锰酸钾可能失去铬酐的许多特性,引发很多问题,因此仍须谨慎选择。2.3球形铝粉的选择及影响本涂料中铝粉含量很高,高温过程使大量铝粉熔融并形成致密的膜,提供了涂料主要的耐高温、防腐蚀(阴极电化学保护)性能;当涂层遭到损伤,暴露面
13、附近的金属铝通过氧化牺牲过程形成氧化铝并逐渐修补损伤面,最终有效修补涂层。因此铝粉的选择至关重要,球形铝粉的耐温高于片状铝粉,通常应用于要求耐温高于500的涂料中,与片状铝粉相比,球形铝粉颗粒中含有大量金属铝,更好地保护涂料,热熔点也更高;更高的铝含量促使涂料在固化过程中有效形成铝的薄膜,有利于获得更加优良的性能。球形铝粉的制造过程通常是:在氮气保护下将熔融的铝通过高速气流气化喷雾形成球形铝粉。不同粒径的铝粉通过不同强度的气流和不同等级筛分获得。在制备过程中生产厂商采用这一工艺的另一个原因是将铝粉表面氮化,形成致密的氮化铝薄膜,降低铝粉的活性并可更有效地保持其形态稳定性;在这一过程及储运过程中
14、少量铝的氧化也是不可避免的。通过这些过程将纯铝含量为99.8%以上的原料制备成了含有95活性铝的球形铝粉。氮化铝和三氧化二铝的熔点远高于纯铝,纯铝的熔点接近700,表面的氮化膜和氧化膜的熔点更高于2000,而固化温度只有550,难于熔融铝粉,但无机树脂磷酸二氢盐在高温或较高温度阶段作为路易斯酸提供氢和六价铬共同作用破坏保护膜,让新鲜的铝粉暴露出来;此外加入的高纯度锡粉在高温下先行熔融,提供铝粉很好的助熔作用,最终获得连续、致密的合金铝层。325目铝粉制备的涂料固化后涂层表面总会出现少量突起,经显微镜
15、观察可清晰地看出是铝,这是因为较大颗粒的铝粉在2h的高温固化过程中不能完全熔融并流平。为进一步改善涂层的外观,根据国外产品规范要求该涂料的细度应小于10m,因此将原325目铝粉换成4号粉(46m),分别为改良配方13,但是铝粉粒径的变化引起了表面积的极大增加,原有的其他材料用量变化很大,尤其是铬酐的用量增加很大,树脂对铝粉的包覆性变差,助剂的用量提高等,这也导致了铝粉在涂料中的比例下降,涂料性能有所下降,通过试验调整,最终获得令人满意的产品。不同规格铝粉对涂层性能的影响见表5。
16、;表5不同规格铝粉对涂层性能的影响24施工工艺的影响
17、0;在摸索过程中发现,涂装工艺的不同对涂层性能的影响很大,刷涂的涂层致密度大于喷涂的涂层,这是因为不同的施工工艺造成了铝粉排列的差异;此外刷涂的涂料黏度大,加入的稀料(蒸馏水)少,表干迅速,提供了铝粉较好的排列,层间差异小,最终形成的涂层致密。选择了4号粉后,因铝粉粒径小导致涂料触变性提高,基本消除了因施工工艺引起的性能差异。3结论通过大量试验制备了水基含铝耐高温防腐蚀涂料,通过性能检测,综合指标达到技术指标的要求。